Background
LiFePO4 (LFP) cathode materials deliver excellent safety and cycle life but offer limited energy density, due to a low operating voltage (3.4V). Introducing manganese to form LiMnxFe1-xPO4 (LMFP) can boost specific energy 10% to 15% by raising the voltage up to about 3.8V, but the sluggish kinetics of Mn²⁺/³⁺ redox require small primary particle size (<200nm) to maintain rate capability. Such fine LMFP powders typically exhibit poor tap and electrode packing density, compromising their volumetric energy density.
Furthermore, the scalability of LMFP synthesis is hindered by strong sensitivities to processing conditions, and conventional synthesis routes like co-precipitation are not cost-effective due to high raw material cost and significant wastewater discharge. For these reasons, LMFP usually exhibits both higher cost and lower volumetric energy density compared to state-of-the-art LFP.
Technology overview
Researchers at The University of Texas at Austin have invented a synthesis process that maintains consistent product quality and performance, leading to reduced manufacturing costs and improved scalability, while eliminating wastewater discharge and allowing for a wide range of low-cost raw materials to be used interchangeably. LMFP cathodes synthesized by this method exhibit improved volumetric energy density compared to LFP.
A mixture of low-purity Fe, Mn, and Li raw materials, such as ore concentrates, is calcined to a LMFO spinel precursor, which is purified by magnetic separation. The LMFO precursor is milled together with additional Li, P, and C sources, plus functional additives and water, to form a slurry. The slurry can be dried in air and heated under N2 to form LMFP particles (~200nm primary crystallites) uniformly coated with 1-3wt% carbon. Optionally, the slurry can be spray dried to form spherical secondary particles with a size of ~3 to 15µm, which exhibit both high tap density (≥1.2g/cm³) and press density (≥2.4g/cm³).
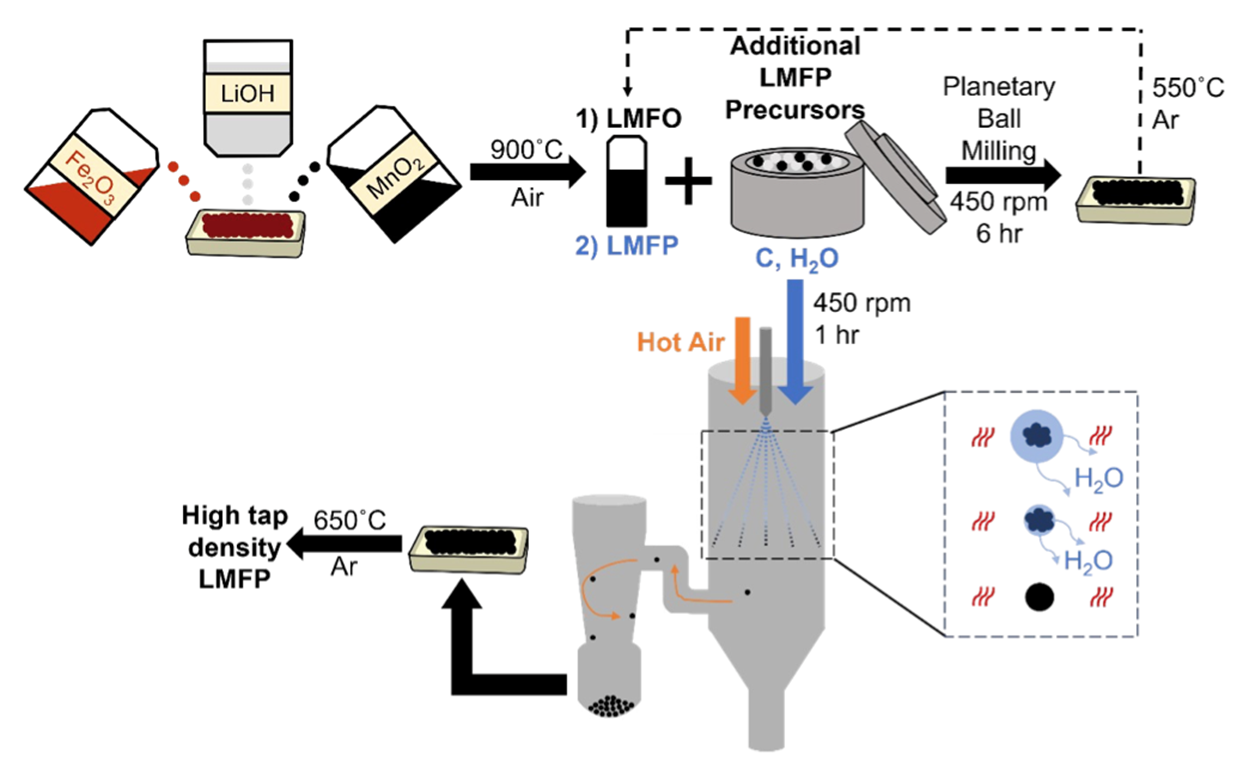
Benefits
- Superior electrode press density: LMFP cathodes synthesized from LMFO precursor (S-LMFP) achieve electrode densities of >2.6g/cm³ with 95wt% active material, surpassing that of conventional LMFP (~2.3g/cm3) and matching that of state-of-the art LFP.
- Improved volumetric energy density: S-LMFP achieves high electrode-level energy density of 1,300 to 1,400Wh L1, surpassing conventional LFP/LMFP cathode materials.
- Enhanced electrode processability: spray-dried S-LMFP secondary particles exhibit a high tap density of 1.2 to 1.5g/cm3 and good mechanical strength, enabling higher loading electrodes and more aggressive calendering.
- Compositional flexibility: the LMFO precursor can be synthesized with variable Fe/Mn ratios of ~40% to 60% Mn, and can accommodate common LMFP dopants (e.g., Co, Mg, V, Ti, etc.) in a single-phase atomically-mixed precursor.
- Scalable, low-cost, wastewater-free synthesis: The two-step LMFO → LMFP synthesis process (solid-state LMFO precursor plus spray drying) is compatible with industry-standard unit operations of mixing, bead milling, spray drying, and calcination.
- Supply chain flexibility: a wide range of low-cost raw materials (e.g., Fe/Mn oxides) can be used to form an LMFO precursor with consistent properties, improving scalability and decoupling raw material selection from product performance.
Applications
- Electrified transportation: Intermediate volumetric energy density, low material cost, excellent safety and lifetime, and exceptional pulse-power make S-LMFP an ideal cathode for electric and hybrid vehicle batteries, especially when combined with traditional NMC cathodes.
- Industrial power tools and equipment: Exceptional pulse power, high safety, and well-balanced performance characteristics are suitable for high-power batteries for cordless tools and automated machinery in industrial settings.
- Stationary energy storage systems: Scalable, low-cost synthesis and high cycle stability enable performance competitive with LFP for grid-scale and behind-the-meter storage.
Publication
S. Reed, K. Scanlan, and A. Manthiram, “Scalable, Low-cost Synthesis of High Volumetric Capacity LiMn0.5Fe0.5PO4 Cathode for Lithium-ion Batteries,” J. Mater. Chem. A, 2024, 12, 21341 (https://pubs.rsc.org/en/content/articlelanding/2024/ta/d4ta03438d).
Opportunity
- This fabrication method reduces battery manufacturing costs by replacing expensive cobalt and nickel with cheaper and more abundant materials.
- Improved battery performance and safety with enhanced cathode design.
- PCT patent application pending, which will be published around October 23, 2025, and will be due for nationalization on October 23, 2026. Available for exclusive license.