The Steerable Flexible Curved-Drilling Robot (SFCR) is an innovative medical device designed to enhance precision in surgical drilling through complex bone structures. This cutting-edge technology features a dual-tube system with a flexible drive shaft, enabling controlled, curved drilling paths that navigate around obstacles like nerves and low-density bone regions.
Background
The use of screw implants for stabilizing bone fractures, reconstructing bone post-tumor resection, and treating degenerative diseases is fraught with challenges. Traditional screw fixation methods often result in complications such as screw misplacement, fractures, and loosening, particularly in osteoporotic bone. Conventional drilling instruments are rigid and constrained to linear paths, limiting their ability to maneuver through narrow, anatomically complex spaces like the pelvis and vertebrae.
These tools struggle to avoid critical structures such as nerves and blood vessels, often requiring drilling through regions of low bone mineral density (BMD), which compromises fixation strength. This rigidity and lack of maneuverability highlight the need for advanced devices that can adapt to anatomical and density variations within bone, ensuring safer and more effective surgical outcomes.
Dr. Farshid Alambeigi and his team have addressed these challenges by developing the SFCR system, which is tailored for precise, curved hard tissue drilling. Dr. Alambeigi, an assistant professor at UT Austin Walker Department of Mechanical Engineering and a member of the UT Austin Robotics Program, specializes in advanced design/manufacturing applications, biomechanical/biomedical engineering, robotics, and intelligent mechanical systems. His research focuses on creating high-dexterity continuum manipulators, soft robots, and minimally invasive surgical instruments.
Technology description
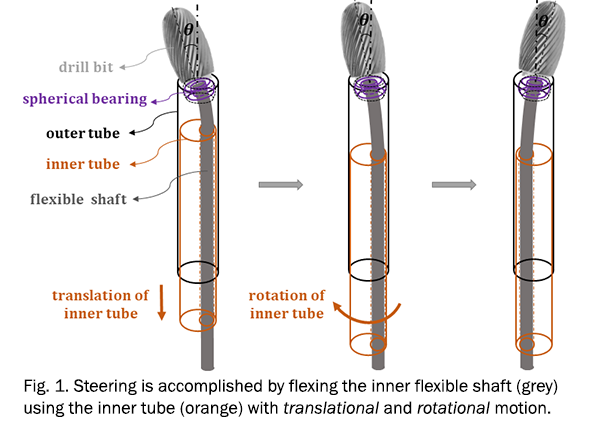
The SFCR represents a significant advancement in surgical technology. It consists of three flexible components: a long shaft with a drill bit at its tip, an inner tube with an eccentric through hole, and an outer tube with a concentric through hole. The drill bit, mounted at the end of the outer tube with a spherical joint, can be actively controlled to orient in any direction. Steering is achieved through the controlled orientation of the drill bit, facilitated by the flexing of the inner shaft and the coordinated motion of the inner and outer tubes. The device allows for variable-curvature 3D curved-drilling paths, enabling precise trajectory planning for complex surgical procedures. The SFCR’s design provides it with superior steerability and dexterity, allowing it to navigate and perform drilling operations in hard tissues with greater flexibility.
Benefits
- Greater maneuverability: enhanced ability to customize drilling trajectories
- Reduced surgical trauma: facilitates smaller incisions and less tissue damage
- Improved implant performance: avoids obstacles and targets desired tissues more effectively
- Complex anatomy navigation: capable of drilling along long curved trajectories in complex bone structures like the pelvis and vertebrae
- Fewer complications: minimizes risks of screw misplacement and nerve injury
- Adaptable to bone density: accommodates variations in bone mineral density
- Enhanced fixation strength: improves overall fixation quality and strength
Commercial applications
- Orthopedic surgery: for complex bone repair and reconstruction
- Bone repair: enhancing precision in various bone treatment procedures
- Minimally invasive surgery: reducing the need for large incisions and minimizing patient trauma
- Robotic surgical systems: integrating advanced robotics into surgical practice
Opportunity
The SFCR has the potential to revolutionize surgical procedures by providing unprecedented control and flexibility, opening new possibilities for minimally invasive treatments and addressing challenges faced by traditional surgical tools. The University of Texas at Austin is looking for an industry partner to license this technology. For more information on the Steerable Flexible Curved-Drilling Robot (SFCR), see the patent details at WO2023023634A1.