Background
Light-driven polymerization methods for 3D printing are particularly attractive due to unparalleled speed and resolution, yet the reliance on high energy UV/​violet light in contemporary processes limits the number of compatible materials due to pervasive absorption, scattering, and degradation at these short wavelengths. Such issues can be addressed with visible light photopolymerizations. However, these lower-energy methods often suffer from slow reaction times and sensitivity to oxygen, precluding their utility in 3D printing processes that require rapid hardening (curing) to maximize build speed and resolution.
Solution
Researchers at The University of Texas at Austin have addressed and overcome the obstacle of oxygen sensitivity in these low-energy methods. Existing techniques may use one or several physical strategies for eliminating oxygen, such as photocuring under inert gas (e.g., N2 or Ar), introducing physical barriers (e.g., in-laminate), employing resins with low oxygen solubility, and increasing irradiation intensity. Despite success in coatings, these approaches limit the general applicability of visible light 3D printing by requiring specialized and costly equipment. Chemical deoxygenation (e.g., oxygen scavengers) presents a low-cost and facile substitute. Using multifunctional thiols (1-10 wt%) as simple additive enables rapid (~10 s/layer), high resolution (<50 μm), visible light (red, ~620 nm) 3D printing under ambient (atmospheric O2) conditions that rival modern UV/violet-based technology. The present process is universal, providing access to commercially relevant acrylic resins with a range of disparate mechanical responses from strong and stiff to soft and extensible.
Results
To determine the impact of thiol additives on the rate of ambient visible light photopolymerization, real time Fourier transform infrared spectroscopy (RT FTIR) was used to quantitatively determine monomer-to-polymer conversion during irradiation. Specifically, the disappearance of the signal corresponding to carbon-carbon double bond (C=C) stretches at ~3,100 cm-1 was monitored using a transmission configuration with the resin sample residing in a ~100 μm gap between glass slides. All samples showed an excellent temporal response, with no identifiable reactions occurring in the absence of light during the first 10 seconds of each measurement. Initially, samples without PETMP (tetrathiol) were irradiated under ambient conditions with a red LED centered at 617 nm (FWHM ≈ 19 nm) having an intensity of 2.5 mW/cm2 (matching the DLP 3D printer intensity). The result was an inhibition period of 49.4 ± 0.4 s and an initial rate of polymerization of 3.6 ± 0.3%/s (immediately following inhibition). Degassing the same resin (no PETMP) with argon for ~1 minute resulted in a significant decrease in the inhibition period, down to 9.8 ± 0.007 s, analogous to prior observations.
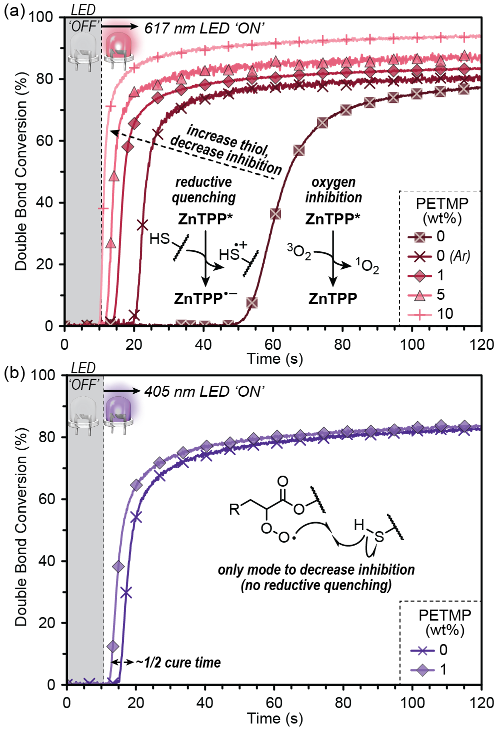
Figure 1: Influence of PETMP (tetrathiol) on oxygen inhibition and rate of BR-741:TPGDA (1:1) polymerization (where PETMP displaces TPGDA), monitored using real time Fourier transform infrared (RT FTIR) spectroscopy. (a) Red light photocuring (617 nm, 2.5 mW/cm2 ) of resins without PETMP under an ambient (oxygen-containing) and inert (argon) atmosphere, and with 1, 5, and 10 wt% PETMP. (b) Violet light photocuring (405 nm, 3.3 mW/cm2 ) using BAPO as the photoinitiator. A decrease in oxygen inhibition occurs with both red and violet light curing, but is more substantial for red light given the combination of reductive quenching and hydrogen atom abstraction by peroxy radicals.
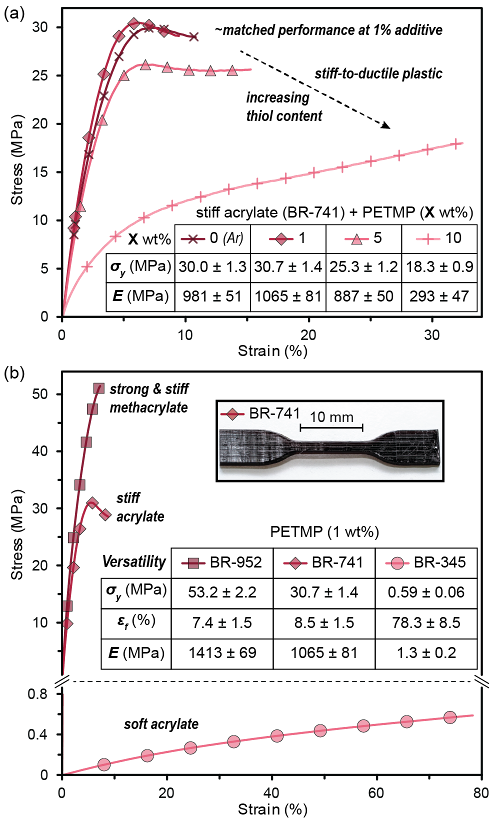
Figure 2. Stress-strain plots of red light 3D printed dogbones (ASTM D638 standard) under uniaxial tension. (a) Influence of PETMP (tetrathiol) content on yield strength (σy) and stiffness (E, Young’s modulus), showing that the high strength and rigidity can be maintained at low PETMP loading and that samples become more ductile at higher PETMP content. (b) Mechanical versatility from ambient visible light 3D printing with thiol additives, from three industrially relevant Dymax®-containing resins. Insets show a representative digital image of the BR-741 dogbone and metrics for σy, E, and strain at fracture (εf).