Background
Similar to how microelectronics transformed computers, microchannel technology has the potential to transform the energy and chemical processing industries by greatly reducing the size of chemical reactor hardware. However, size reduction faces several control challenges. The combination of unit operations (heat exchange, reaction, fluid flow) in a single device results in a loss of degrees of freedom. The reduced dimensions also make it difficult to incorporate distributed sensors and actuators, thus limiting the control of such reactors based on sensing and adjusting channel output and input properties. Thus, there is a definite need for better and faster thermal feedback control.
Technology description
Researchers at The University of Texas at Austin provide an inherently safer design feature for microchannel reactors with bimetallic arrays providing temperature control at the individual channel level. The bimetallic strips are composed of metals with different thermal expansion coefficients thus enabling the conversion of temperature change into mechanical displacement. The arrays are configured to act as thermally controlled valves allowing or stopping fluid flow. The deflection of the bimetallic strips in response to fluid temperature controls the amount of heat transferred through the channel wall to the device. The technology was optimized using Hastelloy X and Incoloy 801 metals and simulations were conducted to test performance using disturbance sequences for transient effects and steady state effects.
Results
Thermally actuated valves are an inherently safer design feature in autothermal microchannel reactors where distributed measurements and actuators are not available. Thermally actuated valves greatly reduces the impacts of disturbances and flow non-uniformity between channels. Additional details may be found at the peer-reviewed article here.
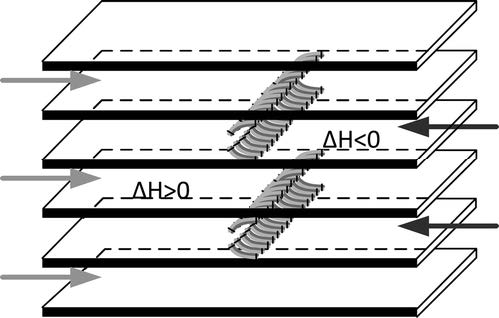
Figure 1. Design of the bimetallic strips.
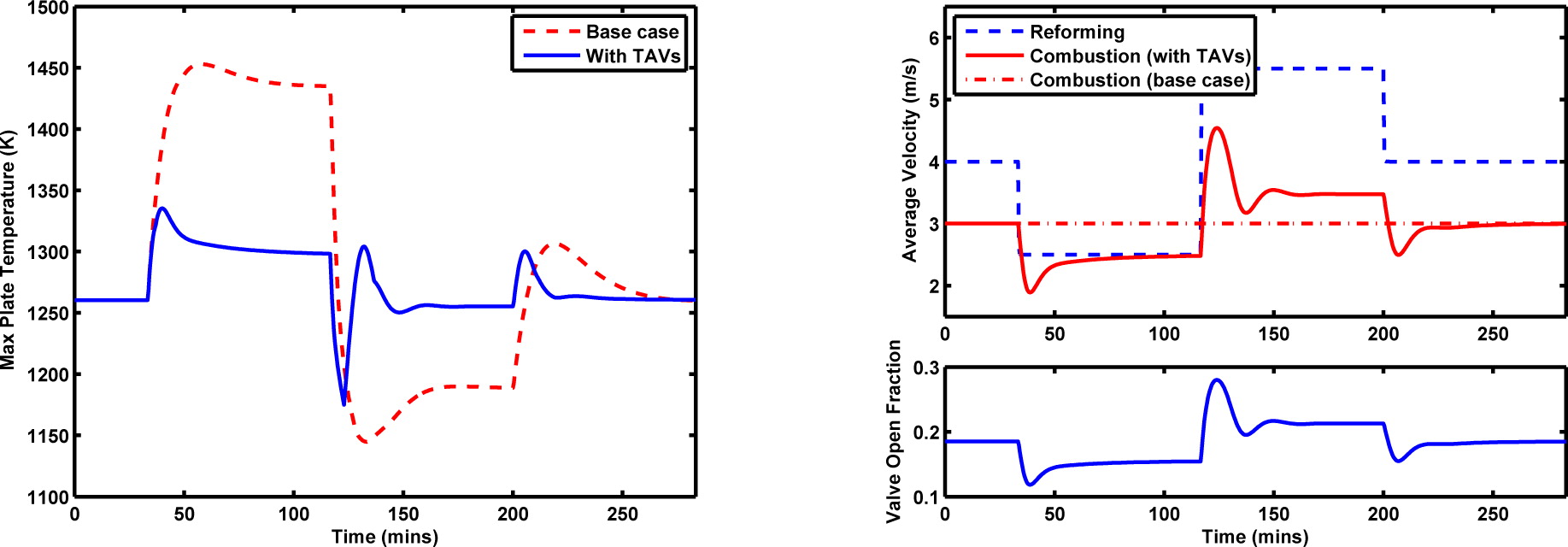
Figure 2. (Left) Maximum plate temperature as a function of time. (Right) Average fluid velocity and valve opening fraction, when subject to a 40% increase followed by a 40% decrease in the flow rate in the reforming channels.