Background
Resin 3D printing has many advantages, such as high precision, smooth surface finish, and rapid printing speed. Conventional LCD or DLP devices use ultraviolet (UV) light to activate photo-initiators in the resin. A cheaper, less power hungry, and more biocompatible alternative would be to use visible light to activate photo-sensitizers in a different resin formulation. However, the use of photo-sensitizers follows a two-step process which limits its speed compared to the use of photo-initiators.
Technology description
Researchers at the University of Texas at Austin have developed a composition of matter to enable fast, high-resolution, visible light photocuring using novel resin formulations. The composition is characterized by an optimal combination of monomers, crosslinkers, and donor/acceptor co-initiators. The technology works by rapidly generating reactive curing agents and recycling the photosensitizer. Specifically, the formulation of donor/acceptor co-initiators enables a photo-redox catalytic cycle which gives rise to fast polymerization. Because the curing agents are generated so quickly and efficiently, the photocuring speeds (less than 1 minute) using this technology rival conventional UV photocuring speeds. Use of such a resin formulation eliminates the need for UV light sources and instead enables photocuring with modular, readily available, visible light LEDs. Devices using this technology should be cheaper both to manufacture and to operate. The researchers have demonstrated the theory with a specific formulation but the technology is not limited to specific components.
Results
This invention offers a simple and low-cost formulation to achieve visible light resin 3D printing. The researchers achieved quick build rates (32.7-45.0 mm/h) and fast cure times (<10 sec), rivaling UV printers while using only a low-intensity (<4 mW/cm2) visible light source. Desirable near isotropic mechanical properties, unperturbed by changing print angles, were also demonstrated. Expanding the space of potential applications, with different resin formulations the researchers were able to produce objects with different chemical and mechanical properties stiff or soft and compliant. Additional features may found in the article at: https://doi.org/10.26434/chemrxiv.12588965.v1.
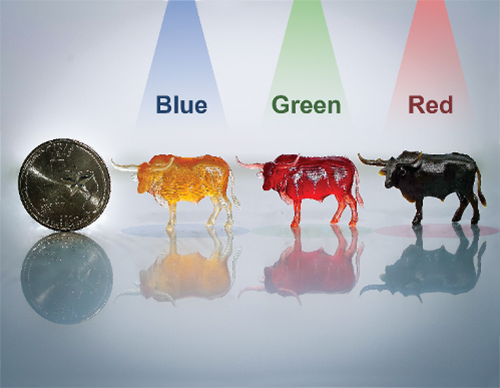 | 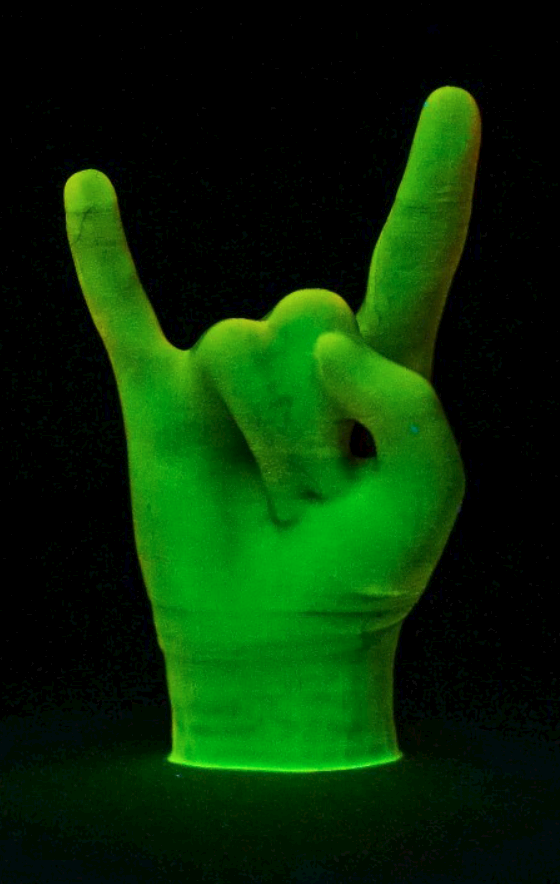 |
Fig. 1: Longhorns printed under various conditions (with coin for scale) | Fig. 2: Example object which is photoluminescent under a black light |
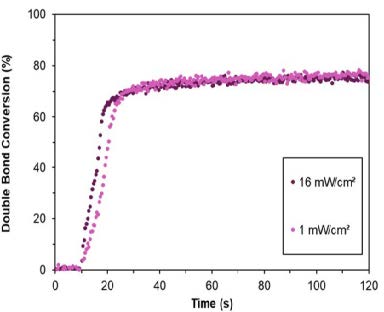
Fig. 3: Acrylic photopolymerization with green light sensitive resin formulation