Background
Ceramics have been found useful in increasingly diverse applications in modern industry because of their high mechanical strength, low thermal conductivity, and high wear and corrosion resistance. In addition, the bio-compatibility of some ceramics allows them to be used for body prostheses, dental, and tissue engineering scaffolds. These types of medical applications are good candidates for additive manufacturing techniques, but current methods either use organic binders and require extremely high temperatures or yield parts with impractically low density and strength.
Technology description
Researchers at The University of Texas at Austin have developed a method to sinter ceramics without the use of binders or extreme temperatures. This is accomplished by sintering while simultaneously applying an electric field. This produces a partially densified part, which can then be brought to full density using a furnace and conventional pressure-less sintering. This method eliminates the post-processing associated with the use of organic binders. This technology makes the manufacture of ceramic parts using additive manufacturing faster and more practical and extends benefits of selective laser sintering—such as complex features, rapid prototyping, etc.—to ceramic materials. Additional information may be found in this peer-reviewed journal article.
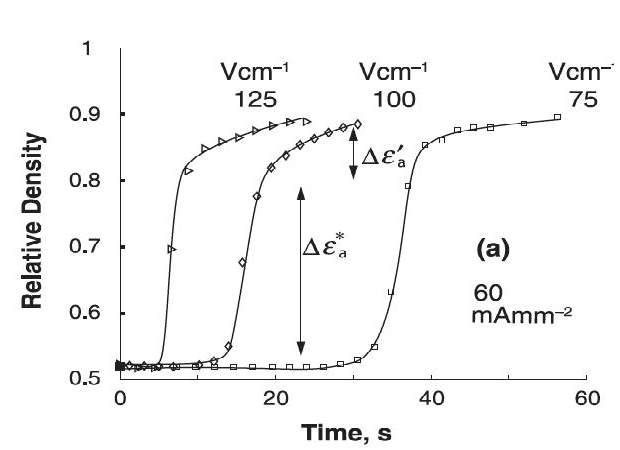
Fig. 1: Densification vs. sintering time for flash sintering at three different DC-applied electric fields
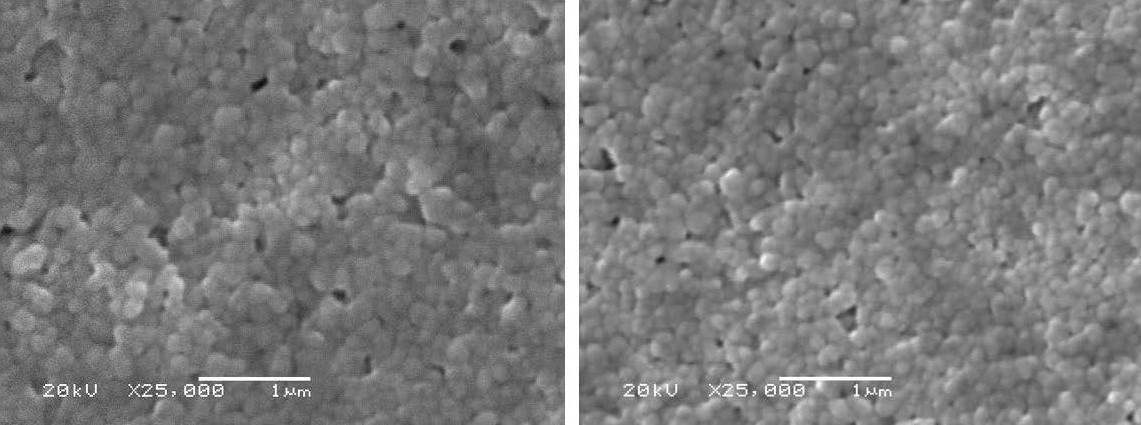
Fig. 2: Surface appearance with (right) and without (left) application of 1000V/cm electric field to yttria-stabilized-zirconia slurry being rastered at 100 mm/sec with 10.5W laser