Problem statement
Currently, heat pipes use a passive wick to pump liquid back from the condenser to the evaporator. The heat transport capacity of these heat pipes is limited by the capillary pressure generated in the internal wick which pumps condensate to the evaporator. Transporting heat over long distances is challenging, since the fluid transport capacity of the wick is inversely proportional to length. Heat pipe technology, which is not limited by wick performance, will be attractive for a diverse range of thermal management application areas, such as solar thermal, defense, data centers, and oil & gas.
Technology description
Dr. Vaibhav Bahadur, a professor at The University of Texas at Austin, and his students have developed a novel conceptualized class of heat pipes, electrowetting heat pipes (EHPs), in which the adiabatic wick section is replaced by electrowetting-based pumping of the condensate to the evaporator. Specific advantages over current technologies include the ability to transport high heat loads over long distances, low thermal resistance and power consumption, and the absence of moving mechanical parts.
This developed technology can be safely conducted in space, and any safety, reliability and compactness-related challenges can be overcome. This planar heat pipe consists of separate liquid and vapor conduits with joined evaporation and condensation regions at the ends as shown in Fig. 1 below. Fig. 2 illustrates prototyped electrowetting device consisting of a printed circuit board as the bottom plate, with electrodes milled from a copper layer, and with a polyimide film as the dielectric layer.
Key benefits and novelty
- Not limited by wick performance
- Transports heat over long distances
- Low thermal resistance
- Low power consumption
- Active electrical control
- Rapidly scalable
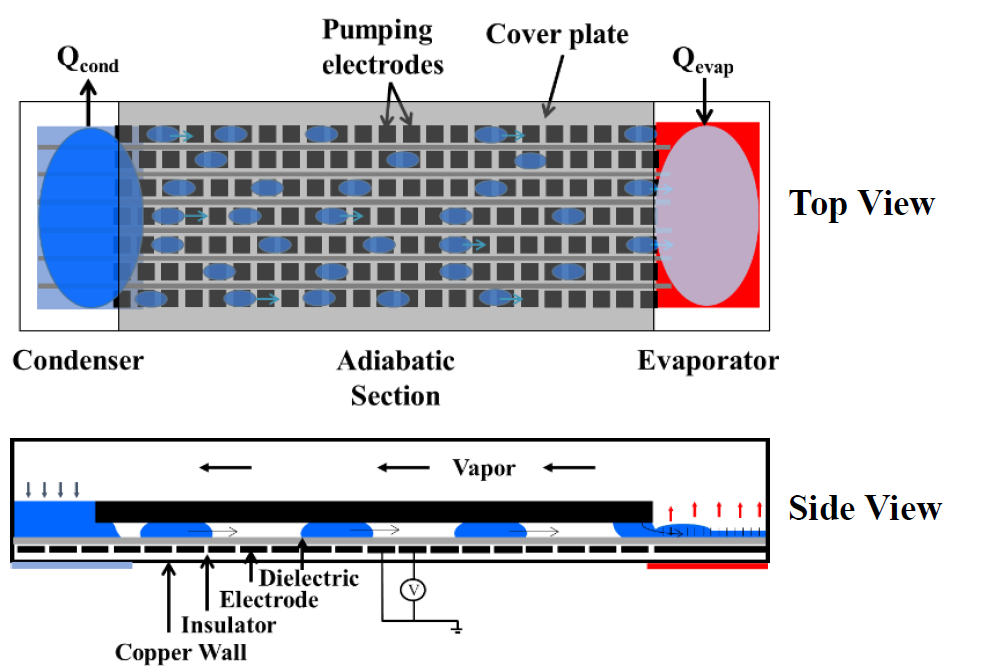 | 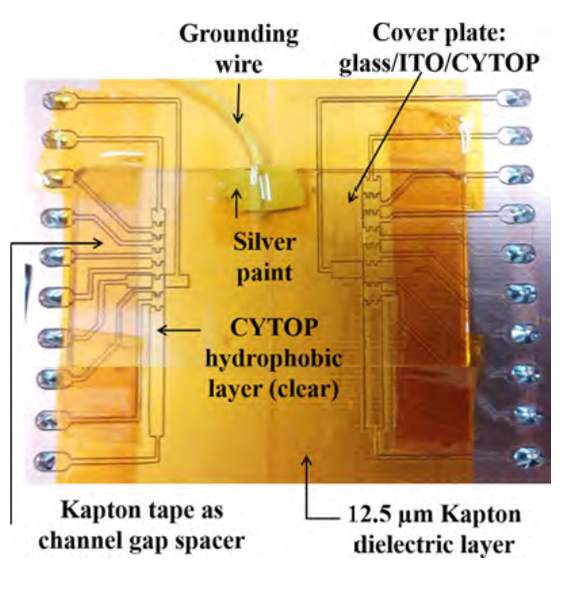 |
Fig. 1: Detailed cross-section view of EHP | Fig. 2: Top view of fully assembled EHP |